Generally, people use both incremental and absolute encoders daily, depending on their requirements.
They mostly use them for servo, heavy-duty, and DC motor-based applications.
There are vast differences between the two that determine which one is more appropriate for your project.
For instance, Incremental encoders are a better choice for simple quality checks and counts. On the other hand, absolute encoders are suitable for systems requiring a precise location for safety reasons and quality checks.
Let us explore these two encoders in greater detail below.
What are incremental and absolute encoders?
Incremental encoder
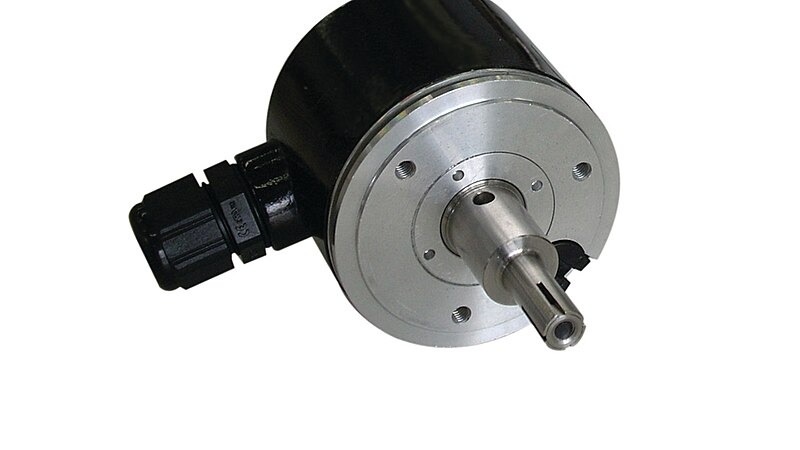
An incremental encoder is a type of encoder that produces an output signal through digital or pulse signals, using
- Circular disc
- Rotating shaft
- Fixed light or magnet
They produce square waves and simple signals to measure the incremental change and position of an object.
Absolute encoder
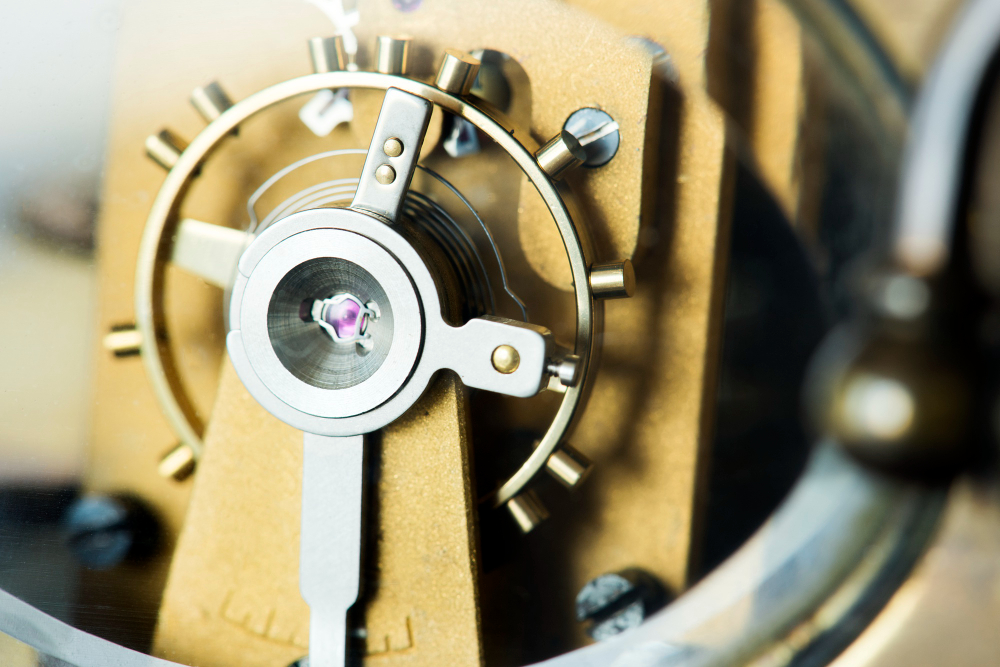
You can use this device to obtain feedback on the speed, position, angular position, and direction of an object.
Absolute encoders provide information about the relative position and absolute position of an object, including after a power outage.
How do these encoders work?
1. How does incremental encoder work?
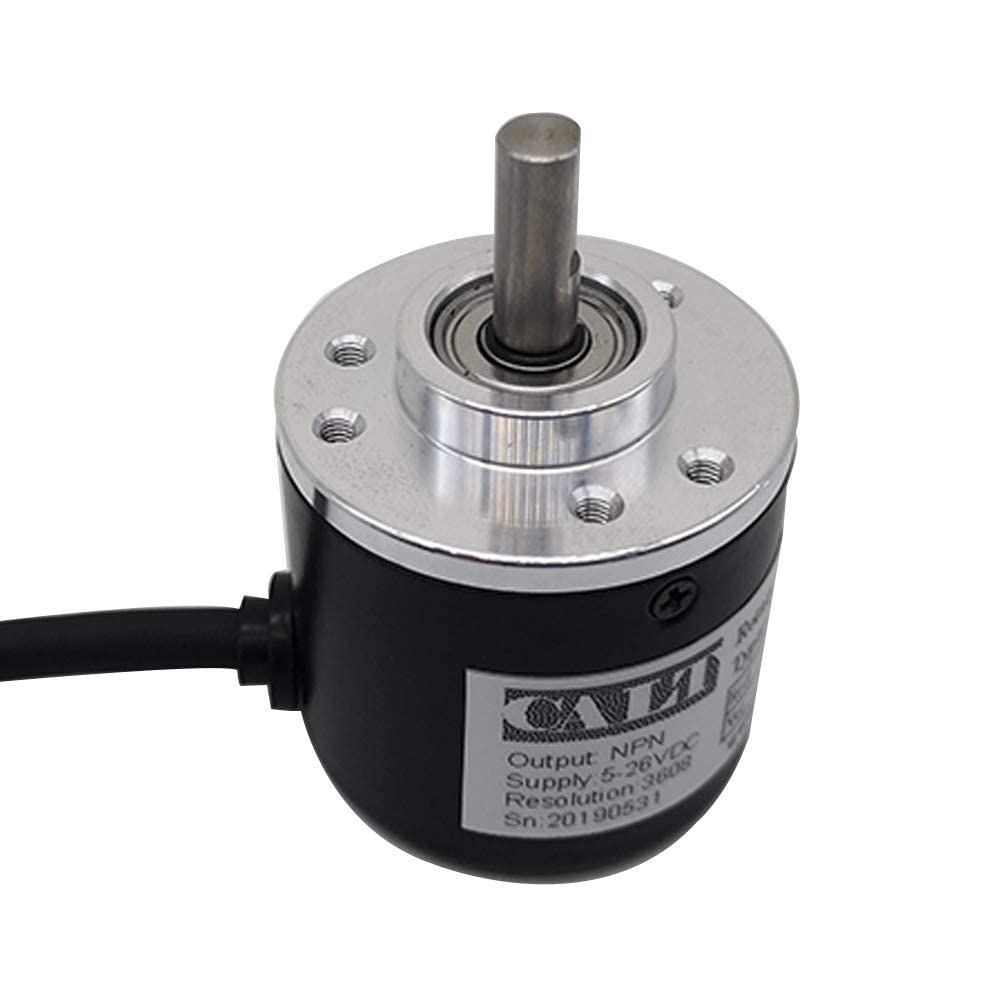
This encoder is much less advanced than an absolute encoder but is still crucial in certain industries. It produces a measurement of position and distance using the relative position of an object and a starting point.
The popular types of incremental encoders are rotary encoders.
Rotary encoders work by positioning a circular and rotating disc in between a fixed light and a transducer, or a fixed magnet. As the disc spins, some slots are positioned uniformly throughout it, resembling the spokes of a wheel.
While incremental encoders will have more uniform slots located throughout the disc, absolute encoders will have more intricate slots decorating the outside of the disc.
The incremental slots occasionally let in a light signal or a magnetic one. It depends on whether a machine is using an optical encoder or an electromagnetic encoder.
As the disc rotates on a shaft, light passes through the opening and is blocked by the opaque areas of the disc.
When light passes through an opening, it hits the transducer on the other side of the disc, producing an output signal that can then be interpreted digitally.
You can control the output signal by measuring the signals per revolution. This measurement by the incremental encoder helps provide information on distance, speed, and position relative to another object.
Most incremental encoders produce square waves, although some of them can produce sine or cosine waves.
A magnetic encoder works in the same way. This sensor will trigger the sensor and produce a square wave when a charge changes, or when a charge remains the same.
2. How does an absolute encoder work?
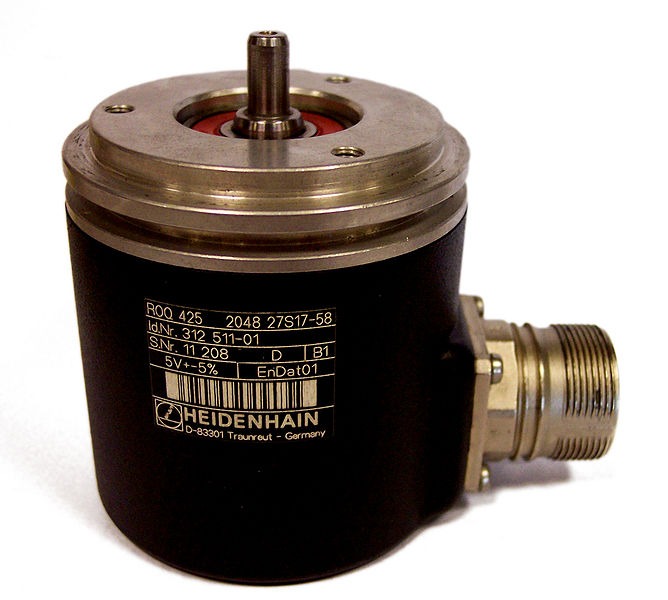
This encoder seems difficult to understand, but knowing its components and how they work can make it a bit clearer. An absolute rotary encoder works by using a rotating disc with slits cut inside them.
The rotating disc is placed in front of a light source and light transducer, like in the case of an optical rotary encoder, or it can be outfitted with a magnetic sensor that detects changes in magnetic energy, just like an electromagnetic encoder.
Both types of absolute rotary encoders make an output signal that is translated digitally into specific information about an object’s movement and absolute position.
An absolute encoder works in the following manner:
- The rotating disc spins around a hollow shaft, allowing light to enter only in areas that have open slits. The rest of the disc is blurry, blocking out light and signals.
- The light enters the disc and moves through the slits of the disc. This light is fixed and is not bothered by outside light sources. Many users use infrared lights for feedback.
- A specific pattern cut is there into the rotary disc of absolute encoders. Based on the signals per revolution, the light being transmitted, or a magnetic signal being interpreted, the transducer in the absolute rotary encoder creates a digital signal.
- The digital signal is brought to another system that interprets the exact position of an object based on the signals received.
Benefits of these encoders
1. Benefits of incremental encoders
These encoders provide many benefits, such as they:
- Are affordable with simple hardware and few sensors.
- Have High-accuracy
- Operate at high speeds.
- Can resist harsh environmental conditions.
- Are easy to use and set up.
- Have flexible scaling functionality
2. Benefits of absolute encoders
The benefits of these encoders are that they:
- Have a unique code for each position, providing precise positioning information without a reference point.
- Can remember their position after a power outage with accurate position data.
- Do not need to be programmed from a new home when powered on.
- Can provide real-time position data, which is useful in systems where it is important to know the exact position of a rotating device before any parts move.
- Have multiple interface options, like analog, Ethernet etc.
- Have higher resolution options than incremental ones.
Wrapping Up
Both the incremental and absolute encoders are great choices for assembly lines that require counts and positional information. So you should decide which type of encoder you need for your working purpose and select one according to that. Best of luck!